Integrated Steel Plant Insight
The Surjagad Ispat integrated steel plant in Gadchiroli, Maharashtra is a significant industrial undertaking, aligned with the vision of Aatma-Nirbhar Bharat. It encompases multiple components including “Sponge Iron Manufacturing”, “Induction Furnace”, “Rolling Mill” and a “Captive Power Plant”.
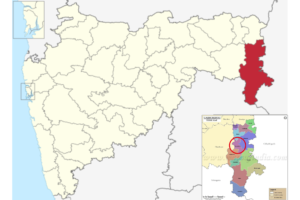
An integrated steel plant combines several key components to streamline production and enhance efficiency
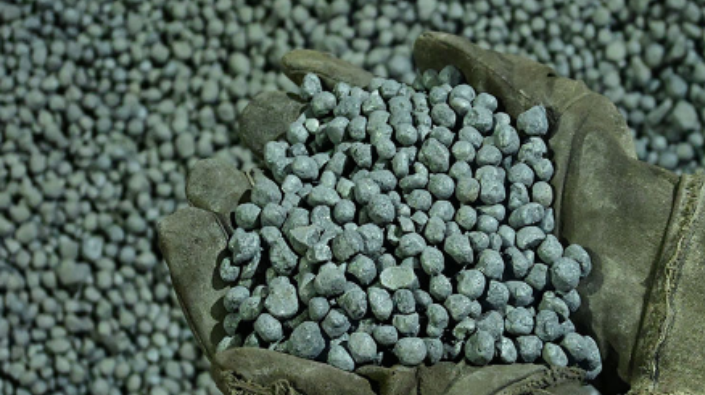
Sponge Iron
The project involves the establishment of Sponge Iron Manufacturing Plant with a total capacity of 2600 Tons per Day-TPD.
Sponge Iron Manufacturing: Utilizes direct reduction of iron ore with coal or natural gas to produce sponge iron (DRI), serving as feedstock for steel production.
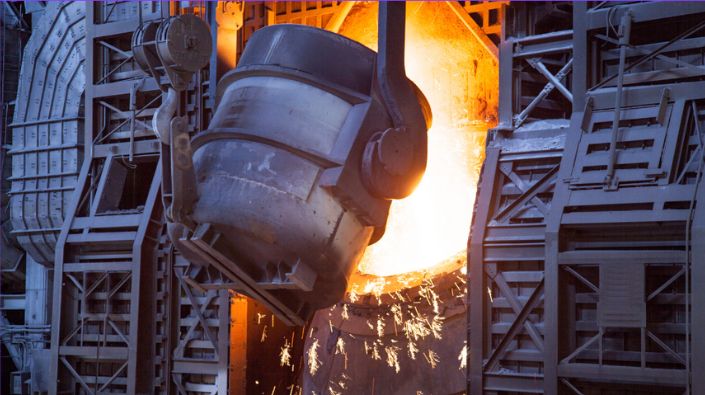
Induction Furnace
An Induction Furnace with a capacity of 8,00,000 Tons per Annum-TPA will be install.
Induction Furnace: Melts sponge iron and scrap steel to create liquid steel, offering energy efficiency and lower emissions, ideal for small to medium-scale production.
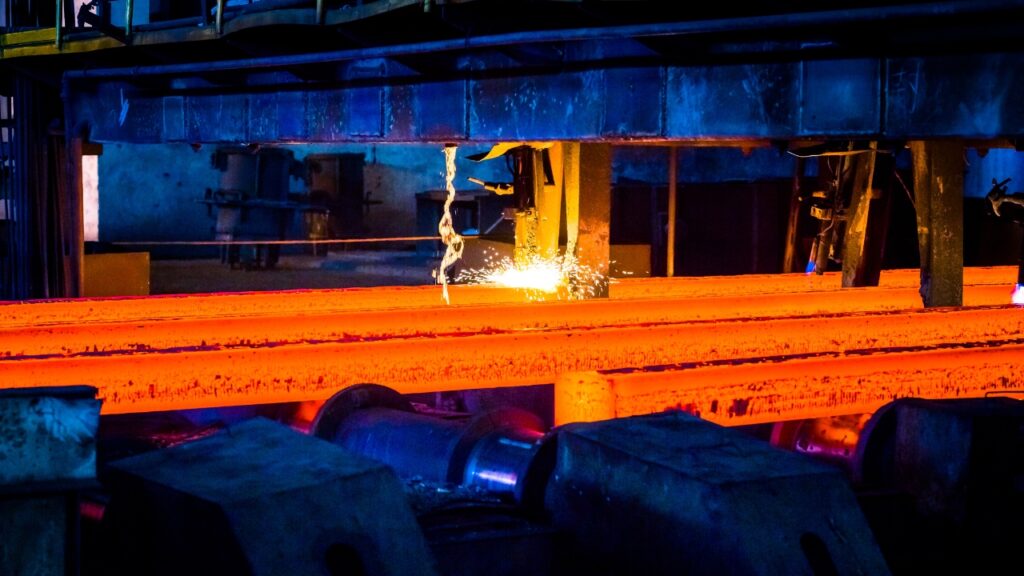
Rolling Mill
A Rolling Mill with a capacity of 8,00,000 Tons per Annum-TPA will be part of our project.
Rolling Mill processes liquid steel into finished products like sheets, bars, and rods using hot or cold rolling techniques, ensuring precision and quality.
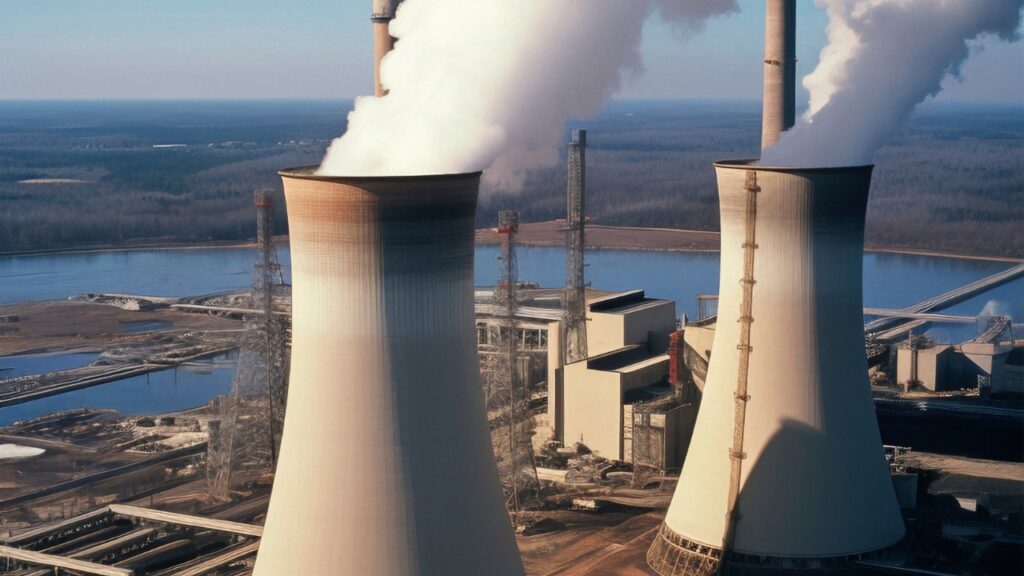
Captive Power Plant
In 150 mega hz Captive Power Plant ensure the stable and reliable power supply for the manufacturing processes.
Captive Power Plant generates electricity for the plant’s operations using waste heat recovery, boosting energy efficiency and reducing reliance on external power sources.
Benefits:
Cost Efficiency: Integrated operations reduce transportation and material handling costs.
Quality Control: Ensures consistent product quality.
Energy Efficiency: Captive power and waste heat recovery lower energy costs.
Environmental Impact: Advanced technology minimizes emissions and promotes sustainability.
In Summary :
An integrated steel plant with these components ensures efficient, high-quality, and sustainable steel production.